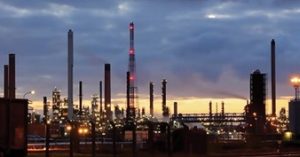
Ensuring environmental responsibility and worker safety in all production units is a top priority for steel companies of all sizes. These facilities use blast furnace, coke oven, and Linz-Donawitz (LD) gases in the production process, the primary component of which is carbon monoxide (CO). CO is not only harmful to the environment: it can be life-threatening to workers. The Flir GF346 uses a specially filtered thermal detector to visualise CO and other harmful gases.
The camera can be used to quickly scan for gas across wide areas and from a safe distance, without interrupting a plant’s production process. CO emissions can be a significant threat to steel manufacturing operations so emissions need to be closely watched. Even the slightest leak in a vent stack or pipe can have a devastating effect.
The FLIR GF346 scans potential leak points rapidly from a distance and allows the user to pinpoint their source in real time. By ensuring there is sufficient Delta T (temperature difference between the ambient temperature at the leaking component and the background scene) technicians can achieve the optimal image contrast needed to detect the lowest level of gas emissions using the GF346’s high sensitivity mode.
A primary use for the Flir GF346 is finding elusive leaks near the casting floor. Often, technicians are unable to detect the CO gas leak source in the casting floor area. Leaks occasionally begin in the late evening hours, so a lack of sunlight and the frequent change in natural airflow direction make it difficult to trace the source of leakage. With the help of a Flir GF346 optical gas imaging camera, inspectors can scan all possible sources of the leakage point near gas piping both inside and outside the steel-making units. The GF346 can find leaks in a variety of scenarios which can be up to 60 metres away from the casting floor.
A facility can develop a routine programme to do pipeline scanning on a consistent basis. Using the GF346 to inspect connections, joints and other potential leak points provides an efficient way to further improve safety within a broader facility footprint and reduce emissions helping the organisation meet environmental stewardship metrics.
Steel industry operators can use the Flir GF346 to inspect blast furnaces, which produce liquid iron for steel making. Frequent leakage of CO gas from the tuyers within the furnaces creates an unsafe and unhealthy atmosphere and inspectors can use the GF346 to scan and identify any leaky tuyers from a safe distance. If a leak is discovered, operators can take immediate corrective action.
A key advantage in using a Flir GF346 for LDAR inspections is, according to Flir, the high Return on Investment of the technology. Gas leaks can cost money in a variety of ways: lost product, added safety expenses, and increased downtime.
The Flir GF346 OGI camera can serve as an extremely important tool for steel companies, helping inspection crews identify problems before they become catastrophic and conducting surveys without shutting down operations.