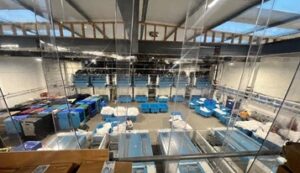
HID, the worldwide pioneer in trusted identity solutions, announces that Royal Jersey Laundry has introduced a new tracking feature of HID’s linen management platform at each of its 5-star hotel customer sites to guarantee that drivers drop off and collect precise linen stock and that costly errors are avoided. This new feature replaces a paper-based system used by drivers for the management of cages filled with clean/soiled linen delivered/collected at customer sites.
It provides detailed end-to-end tracking of linen cages across multiple customer locations throughout the whole cycle of washing, packing, delivery, and collection, a complex process given that 550,000 pieces are laundered each week for numerous clients.
Founded in 1915, Royal Jersey Laundry is one of the few cleaners servicing the luxury hotel sector. Based in a 25,000 square-foot purpose-built facility in Dagenham, rebuilt in 2021 for £15 million after a fire, it works with most five-star hotels in London including The Dorchester, The Carlton Tower Jumerah, The Peninsula London, and The Ritz.
Supporting the five-star segment is demanding given the constant communication required between the hotel and laundry, exacting standards, and the quantity and range of items to be laundered.
This includes duvets, sheets, towels, and bath robes along with smaller items such as foot mats, drink coasters, shaving towels, and dry cleaning for guests themselves. Royal Jersey Laundry operates 24/7, employs 150 staff members, and washes 40 tons of linen per day.
In contrast with budget and mid-level hotels, five-star hotels prefer to use linen they own with five sets kept of everything, allowing them to maintain a rigorous laundering schedule and ensure guests always receive fresh, cleaned linens.
“An average 300-bed hotel will have around 30,000 items of linen which will cost around £250,000,” says James Lincoln, Royal Jersey Laundry’s managing director. “The volume of linen is so high and it’s always moving such that accurate inventory control was a major challenge verging on the impossible.”
Before the HID cloud-based RFID linen management system, everything was done manually. Laundry staff would check items off ironing/folding machines, a wholly error-prone process, and log the quantities on pieces of paper.
The operational overhead for the laundry was exacerbated as the various linen items from the different hotels had to be kept separate, too. “Linen is everywhere: on beds, in cupboards, in transit, and at the laundry, yet no one had full insight into stock levels and, when things went missing which often happened, typically we’d get blamed,” says Lincoln.
To address these problems, Royal Jersey Laundry installed a real-time linen inventory management system from HID combining LinTRAK® RFID tags, a full set of RFID equipment including table-top and conveyor-belt scanners, one RFID portal and one cabin scanning unit, and cloud-based Acuity software.
The discrete LinTRAK tags are sewn into linen items by laundry staff or linen manufacturers during the production process. Some hotels also use LinTRAK tags to manage staff uniforms and restaurant linens such as napkins and tablecloths.
Around 40% of Royal Jersey Laundry hotel customers have transitioned to the HID linen management solution and connect via Acuity’s web portal. Once cleaned, the linen is packed into cages, and scanned in seconds through HID’s RFID cabin station.
Items are automatically counted, with delivery notes generated including billing information. HID’s Acuity software integrates with the laundry’s Sage accounting software to generate invoices.
The implementation of HID LinTRAK textile tags, RFID stations, and the Acuity software platform has radically changed how Royal Jersey Laundry operates, delivering a range of benefits:
● Fast Return on Investment: Since the installation of the HID equipment in 2019, the system has already paid for itself given the efficiency and productivity gains.
● Better use of people resources: Laundry and housekeeping staff no longer waste time on dull and resource-intensive activities like manually counting linen. They have been redeployed to more productive work, generating 10-20% savings in labor costs.
● Better visibility of stock levels: As hotels know exactly the location and quantity of linen, they are better able to cater to peak demand, reducing linen expenditures by up to 30%.
● Improved responsiveness and customer satisfaction: Access to in-depth data generated by the Acuity platform means the laundry can quickly answer customer queries. “We give hotels complete transparency about where their linen is in the cleaning and delivery cycle. There are just no grey areas anymore,” says Lincoln.
● Increased security of expensive linen assets: While theft of linen at five-star hotels is rare, it does happen. RFID tagging enables better monitoring of expensive bedding and towel investments.
● Enhanced reliability and productivity: Operations are more efficient as RFID-enabled items can never be lost or misplaced. Furthermore, digital scanning results in faster processing of items. “We’re effectively two businesses: the laundry itself and a logistics operation. We run a mixed fleet of lorries and electric vans which nip in and out of London three times a day picking up and delivering garments for hotel customers using us for guest work,” adds Lincoln.