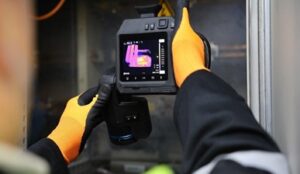
When production halts unexpectedly, it disrupts the entire supply chain, causing delays in product delivery and potential loss of customer trust. Financially, the costs can be substantial, including lost revenue, overtime pay for workers, and expenses for emergency repairs. Additionally, frequent downtime can damage equipment, reducing its potential lifespan and increasing maintenance costs.
Thermal imaging, also known as Thermography is a powerful tool for preventative maintenance in manufacturing. It involves using infrared cameras to detect heat patterns and anomalies in equipment.
By identifying areas of excessive heat, which often indicate potential failures, thermography allows maintenance teams to address issues before they lead to costly unscheduled downtime. One of the key benefits of thermography is its non-invasive nature. Thermal imaging is performed while equipment is operating, minimising disruptions to production.
This proactive approach helps in identifying problems such as electrical faults, mechanical wear, and insulation failures at an early stage. Consequently, it enhances the reliability and efficiency of machinery, extending its lifespan and reducing maintenance costs.
Moreover, thermography provides valuable data that can be used to track the condition of equipment over time. This data-driven approach enables more informed decision-making and better planning of maintenance activities. Overall, thermography is an essential component of a robust preventative maintenance strategy, ensuring operational continuity and safety.
Teledyne FLIR is a major company specialising in the design and production of thermal imaging cameras and sensors. Renowned for their innovative technology, FLIR’s products are used across various industries, including manufacturing, security, and environmental monitoring.
FLIR cameras are sophisticated instruments that can appear daunting to the untrained user, with specialist applications requiring a deep knowledge of thermography to provide valuable insights. On the other hand, FLIRs thermal imaging cameras can simply be viewed as tools to do a job, and that job is to inform maintenance teams about the condition of critical assets. The information can provide information to predict the maintenance required, prevent failure, and avoid unscheduled downtime.
While training can be provided by organisations such as the Infrared Training Centre, or online via the FLIR Academy; FLIR offers multiple features to support both experienced and inexperienced thermographers in monitoring their equipment.
For example:- the FLIR Exx-series and Txxx-series of cameras can be set up by an experienced user to follow an ‘inspection route’, then less experienced or even beginners can follow the same route, with the camera guiding its operator to take accurate and usable images, pre-selecting the settings and parameters as required. At the end of the inspection, the thermal images can be synced wirelessly to a pre-prepared report, allowing easy analysis and interpretation.
This might all sound complicated, but it is just a process that once set up, supports inexperienced thermographers to capture data in a meaningful way. All are designed to provide insights into the condition of equipment around a factory, production plant, or manufacturing facility.
If the maintenance teams are forever ‘fire fighting’, on high alert, or waiting to react urgently to equipment failures, then it’s time to invest some more time and energy to get ahead of unplanned downtime and monitor the condition of the equipment.
One of the best ways to do this is through thermal imaging which can be as affordable as companies need it to be, with training, or guided inspection tools readily available to meet the requirements of the technicians and engineers responsible for maintaining equipment uptime.