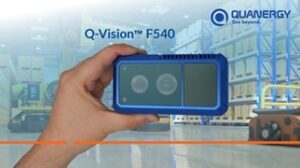
The newly launched F540 3D iToF Lidar sensor from Quanergy joins the company’s Q-Vision solid-state family of sensors and extends beyond Quanergy’s acclaimed mechanical M-Series line to optimise automation processes across industries such as logistics and warehouse management, construction, and agriculture with cutting-edge solid-state technology.
The F540 promises exceptional environmental and vibration performance for both off-road and indoor industrial vehicles, including forklifts, Autonomous Guided Vehicles (AGVs), Autonomous Mobile Robots (AMRs), coupled with its exceptional imaging quality, edge compute intelligence and highly accurate volumetric measurements.
It also offers an advanced low-noise point cloud and high resolution, allowing developers to detect objects and critical features—such as pallet pockets, shelves, tables, and doorways—at longer ranges with superior precision compared to existing solutions. This increased accuracy and clarity enable faster and safer operations, enhancing the efficiency and economic return of automation processes.
The Q-Vision F540 is presented as an essential tool for delivering reliable situational awareness in AGVs and AMRs, supporting a wide range of critical applications, including pallet pocket detection, collision avoidance, object classification and navigation.
And, according to the company, with 75% more data points than leading competitors, the F540 redefines industry standards in high-resolution 3D Lidar technology. Its advanced on-sensor Image Signal Processing (ISP) significantly reduces noise, delivering a crisp and reliable 3D point cloud that streamlines and accelerates engineering workflows.
The Q-Vision F540 is designed to overcome key obstacles that have traditionally hindered the widespread adoption of 3D Lidar in AGV and AMR markets. It directly addresses issues such as:
● Limited field of view (FoV) and low resolution in existing iToF cameras
● Lack of plug-and-play functionality, requiring extensive software development
● Absence of developer-friendly software tools
● High costs associated with off-board point cloud processing
● Data transport challenges with edge compute for at-sensor insights
● Inability to perform in challenging environmental conditions, such as bright sunlight or specific indoor lighting, and able to withstand high shock and vibration
● Short-range performance limitations (dead bands)
● Inability to read barcodes or QR codes
In addition to resolving these issues, the F540’s on-sensor software tackles common iToF Lidar challenges such as reducing the interference of stray light from reflective surfaces, outdoor operation under sunlight, eliminating false data from distances beyond the sensor’s set operating range, high dynamic range adaptation, disturbance from other sensors close by and motion blur.
These capabilities, combined with low cross-sensor interference, allow the F540 to be deployed effectively in environments with multiple robots operating simultaneously. The sensor’s wide field of view ensures comprehensive situational awareness, while its high angular resolution enhances precision in object detection.