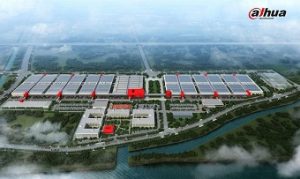
To grasp the current manufacturing trends and seize the Zeitgeist of Industry 4.0, a new smart IoT industrial park in Hangzhou has been put to use by Dahua Technology.
Dahua Smart (IoT) Industrial Park occupies in total 512 acres in Fuyang district of Hangzhou, about 20 minutes’ drive from Dahua headquarters, designed to host 6000 staff. With topnotch technologies, personnel, materials and other benefits, Dahua’s smart industrial park will bring productivity and quality to a brand new level.
The automatic production solution based on integrated information system not only grants a higher productivity that significantly shortens the delivery cycle time for Dahua customers, but also a greater flexibility to specialized requests and ever-changing reality.
The employment of software such as ERP, PLM, PDM, MES, APS and WMS helps to achieve information integration, which, combined with industrial cameras, RFID sensory technologies and automation technologies, can integrate personnel, logistics, works, engineering projects and finance from respective sections of production(preparation, assembly, testing, packaging, inspection, shipment), rendering the whole process visible, traceable and digital.
The faster speed also applies to the development of new molding, since Dahua smart industrial park provides the great benefit of internal synergy, allowing the end-to-end vertical supply chain with marketing, R&D and manufacturing efficiently integrated. The advanced organizing system is supported by topnotch equipment while also supporting CAD / CAM / CAE collaborative development and simultaneous manufacturing.
Higher quality saves lots of time and economic costs for clients. Even more importantly, higher quality results in less likelihood for products to malfunction especially when they are used in critical, not-allowed-to-go-wrong situations. Dahua’s products are guaranteed with a higher quality for two reasons: first, Dahua has set a high standard of accuracy in production; second, with a reliability lab at the production end, Dahua has put together an effectively closed loop for quality control in the manufacturing process.
Accuracy has always been one vital index defining the manufacturing ability because it directly sets the limit to quality and range of products to be produced.
Dahua industrial camera plays an important role in IoT, providing a closed loop for quality control in the manufacturing process, in which all materials, personnel and devices are connected and products are traceable to the specific production line and precise time it got made. Boasting a variety of functions, Dahua industrial cameras are used in different sections of production, enabling automatic assembly, high-precision graphic inspection and product flaw inspection. Through high definition machine vision, Dahua industrial cameras automatically and precisely locate the components, limiting the assembly error to micron level. Equipped with enhanced vision and intelligent analytics algorithm, the industrial camera can spontaneously detect and recognize flaws in the performance and outlook of products, thus promising not only the volume of cameras production but also the steady quality of each and every one of them.
Reliability must be put to test, in R&D as well as in manufacturing process. The reliability lab at the production end serves to assure quality by randomly taking products from production lines and put them into reliability tests simulating falling, high/low temperature, worn-out conditions, which are conducted by industry leading testing equipment in the lab. Thus what’s conceived in R&D is confirmed from the production line, the synergy of both ends promising better products (for common use or specialized needs). This lab is also responsible for testing all the raw materials. Thanks to the aforementioned information integration, all tests are automatically conducted, recorded and traceable.